By 2029, Green Carbon Solutions’ designed charcoal will concentrate the soil, cleanse the water, and generate electricity using “all the last piece from the wood piece.”
Indian Town, Fla. – Martin Ellis says it will boost domestic production of silicon chips, solar panels and steel while enriching soil, purifying water and generating electricity.
The veteran entrepreneur will do this in a centuries-old process that refined a product man that has been used for thousands of years in a specialized production plant tested in Poland, and moved to a 17-acre pasture in Swamp Savannah, South Florida.
A key component of this high-tech venture?
“If you want to make good silicon, you need a good ‘coarse’,” Ellis said, referring to the fine sands of Myacca, the official state soil of Florida.
He then added “wood” in particular “wood” from eucalyptus trees developed by forest geneticists at the University of Florida, and “wood” converted into biochar using pyrolysis, heating or pyrolysis of organic materials in the absence of oxygen.
“Our DNA has 30 years of experience developing pyrolysis to meet the needs of large European silicon customers,” Ellis said. “Our history is how we put them all together.”
“We’re a bit unique,” Ellis said. “There’s nothing like this. A bio-based sustainable low-carbon business that utilizes Florida resources,” which allows you to produce high-quality biochar on an industrial scale.
Decarbonization is no longer a priority under the Trump administration’s energy policy, but industry and entrepreneurs such as Ellis are investing billions in new and ancient technologies recycle biochar, biomass and more for expanding carbon-free applications.
A broader biomass market is also growing, using raw plants such as corn to generate electricity using ethanol, “waste,” solid waste from landfills, and methane-rich sewage sludge from utilities and cattle ranches.
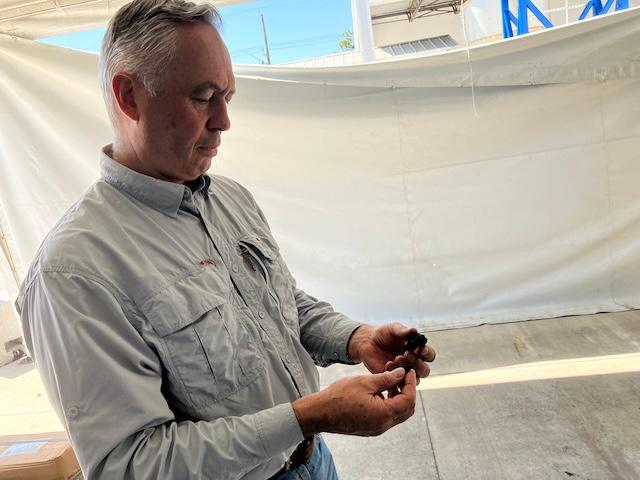
President Martin Ellis, founder of Green Carbon Solutions, will investigate “engineering charcoals” his factory in Indiantown, Florida, produces from eucalyptus wood for a US-based silicon chip maker. John Housey/Epoch Times
Just the beginning
Ellis, 60, from South Africa, has decades of global experience as an executive and consultant as president/CEO of Zurich-based Fairchild Society, Stern, Stewart & Company in New York, and Ohio Information Technology Leader Agilily Shee.
Since leaving Agilysys in 2011, he has focused on energy development, particularly for silicon chip manufacturers, pyrolysis technologies that can produce low-emission, high-carbon reducing agents for the alloy industry.
Established Green Carbon Solutions, Porter board chair, Ellis is also the board chair as a commercial service that pioneers the Norwegian company carbon capture and storage, and which customers pay fees based on the amount of carbon released and captured.
He didn’t invest and manage Green Carbon Solutions’ startup biochar operations if he wasn’t sure there was a market for his products.
And it’s now a biochar for US silicon chip makers. “For over 15 years, it’s been about making the supply chain more sustainable for the domestic industry,” he said.
The silicon is “at the top of the metal pyramid,” Ellis said. He said that silicon in semiconductors must be extracted and purified from compounds such as silica sand throughout the manufacturing process to achieve the required purity.
Eucalyptus has been a commercial crop in South Florida since the 1960s, but the collapse of the pulpwood market since the 1990s led to casualties in the digital age reducing demand for newsprint.
His interest in eucalyptus was primarily as an energy source. This is because those same attributes make them ideal biochar. He and others at the University of Florida considered the possibility to be a short-term wooden crop, a fast-growing tree that can be used in advanced manufacturing.
“Eucalyptus can make consistent products every day,” Ellis said. Green Carbon Solutions states that it can “use waste.”
Green Carbon Solutions has a contract to sell biochar to Mississippi Silicon and Sinova, Kentucky. It will ultimately be sold to solar panel manufacturers, automotive/aircraft manufacturers, medical device companies, construction industry and more.
But that’s just the beginning.
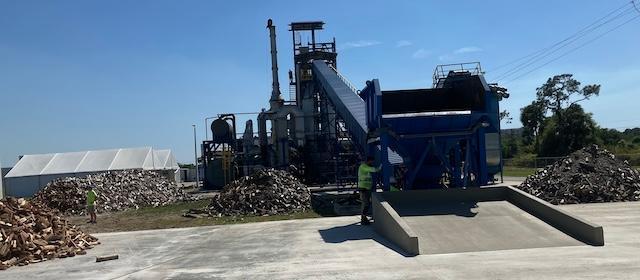
The Green Carbon Solutions plant in Indian Town, Florida, in mid-March is preparing for “continuous production” by summer. John Housey/Epoch Times
It works and ready
Ellis found Indian Town in 2019, a drive-by perspective 40 miles northwest of West Palm Beach. Not only is it “coarse,” it also spans the CSX railroad line near Florida’s 710 “Bee Highway” and the Port Everglades.
The first phase of his project is almost complete with a roller coaster, with the construction of a 4,145 square feet of office complex and a horizontally moving grid, four dryers, and a high 110-foot retort structure with an electric arc boiler at a glance from afar.
“We know it works,” Ellis said in mid-March. “We did a test and knocked out the rough edges. We’re ready.”
Within 18 months, Ellis said the site will generate its own power.
“We do that in Poland,” he said. The emissions were used to generate steam. “Industrial self-sufficiency. We don’t get anything from the grid.”
He said they might eventually sell “extra power.”
The plant produces activated carbon, which is used to clean the water, and is very expensive, Ellis said. Germany has a pilot project to test the green carbon solutions of its products.
He said the company will sell bio-oil for a variety of uses. Farmers praise Biochar ash because they retain more water and nutrients than other biomass and help reduce the runoff that grows red tides and algae flowers in Florida.
“It’s a integration of technology and experience, and it’s cutting edge for entering a new arena. Putting it all together, you get an interesting mix of revenue streams from the processing of biomass,” Ellis said.
He has another way: “You took all the last pieces out of the wood pieces and turned them into something useful.”
Green Carbon Solutions has 10 employees, doubled by the end of the year. For the next 18 months, Ellis said he would expand to 40 workers and add staff “gradually” until 70 will be needed by 2028-29.
In mid-March, the control room was still resident by Polish engineers, including Martin Moylinz and Jansawitz, who dismantled it and put it back in place.
“Now, that’s easy,” Morinz said.
“There’s a lot of Polish sweat here in the soil,” Ellis said.
But most of their work is done. The “turnkey” plant is ready to operate at full tempo.
“The cows were here a few years ago,” Ellis said. “We’re in a good place.”